Hello,
I agree there is still much to be said for on-site construction versus factory made house sections. Our company, Noble Home, creates affordable house kits, which are assembled/built on site by a builder or owner. With a building system and kit of parts, designs can be site specific and can be much more sustainable than a typical prefab which are generally non climate responsive. The design and kits average about $50 per square foot, but do not include interior finishes.
Blog Post
Can Prefab be Green and Affordable?
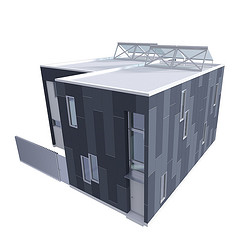
- Prefab is more affordable
- Prefab produces less waste
- Prefab takes less time
- Prefab is more "Green"
Published September 17, 2008 Permalink Citation
(2008, September 17). Can Prefab be Green and Affordable?. Retrieved from https://www.buildinggreen.com/blog/can-prefab-be-green-and-affordable
Comments
Hello, I agree there is still
I own a prefab home because i
I own a prefab home because in central New Hampshire, Epoch was the only builder able to give me an energy star home. Yes, it was more expensive than stick built initially but it was more solidly built (20% more wood) than a stick built home of the same square footage and that has value. We also enjoy much lower energy bills than our stick built neighbors and our home is more sound proof and those attributes have value. Having been in my home 8 years now, I consider the price difference a wash and now have bragging rights over my neighbor's energy bills. I encourage people to take the longer view of the 'cost' of these prefab homes.
Add new comment
To post a comment, you need to register for a BuildingGreen Basic membership (free) or login to your existing profile.