Congratulations for this invention! It is indeed contributing to the revolutioning of this kind of constructions.
Blog Post
Bensonwood Reinventing the House
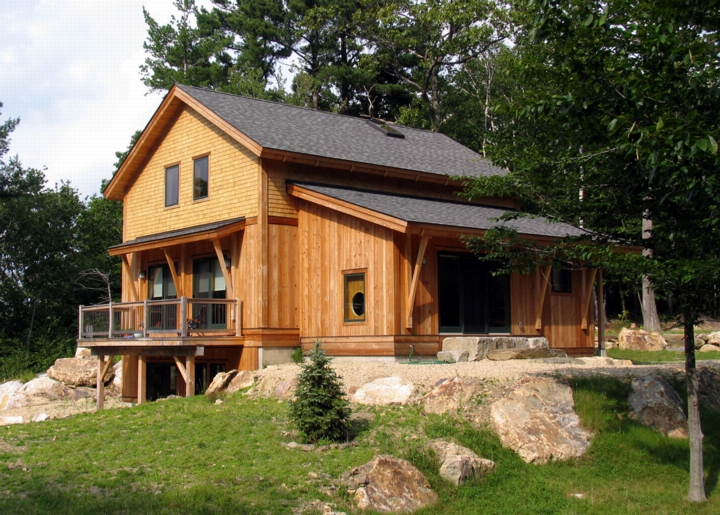
I had the good fortune last week to spend a few hours touring the Bensonwood offices and factory in Walpole, New Hampshire. I've known Tedd Benson for perhaps 20 years, and knew of him a lot longer than that through his writings. He pretty-much created the modern timber-framing profession, starting back in the early 1970s when he set out to reinvent the craft of timber-frame construction that our New England ancestors used centuries ago. His 1980 book, Building the Timber Frame House, and several others since, have inspired many of us for their vision, beauty, and rugged durability. In recent years, Benson has shifted his primary focus away from timber framing (though that's still an important part of what his company, Bensonwood, is all about). His Open-Built® construction platform, inspired by the work of Open Building pioneer John Habraken and supported by MIT's Open Source Building Alliance, has gone a long way toward bringing down the costs of the top-quality homes his company builds.
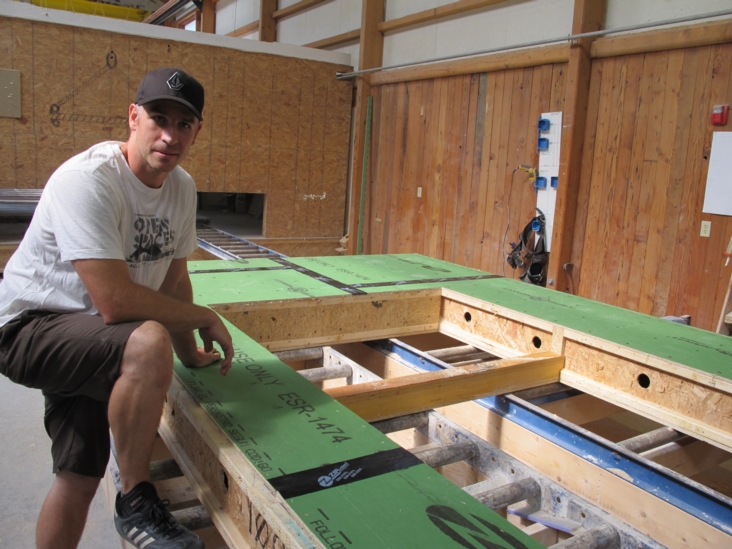
Unlike the old days, when each of Benson's homes was custom-designed from scratch, the new Bensonwood Lifestyle series is built on a modular platform with pre-engineered components that can be used to create homes ranging in size from 800 square feet to over 4,000 square feet. This system is called the 3BMatrix? (3B for "Bensonwood Building Block"). The company uses advanced Swiss "building information management" (BIM) software to put these 3BMatrix modules together in 3D models. Then fabrication instructions are transmitted to their German Hundeggercomputer-based machinery that cuts the components to precise dimensions for factory-panelizing.
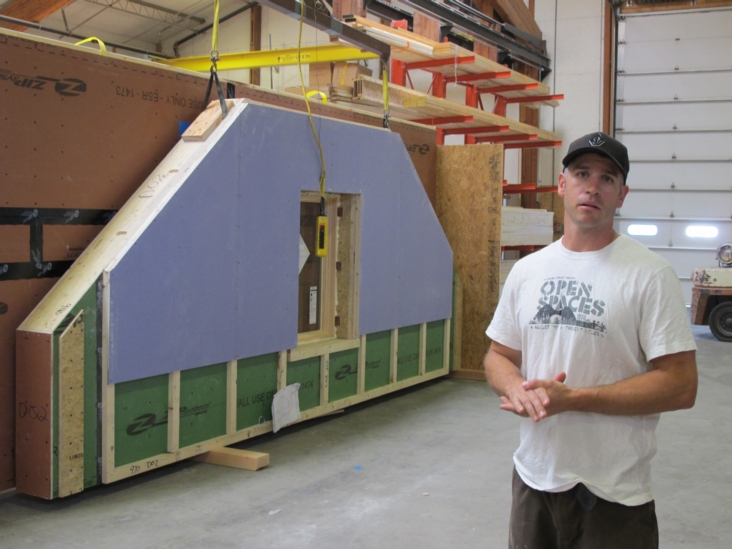
Bensonwood's OBPlusWall I've visited modular home and panelized construction factories before, but what sets Bensonwood apart for me is the attention to energy performance, green materials, and rigorous building science. At the heart of this system is the OBPlusWall (OB for "Open-Built"). These factory-built (panelized) walls are framed using 9.5-inch-deep I-studs filled with R-35 dense-pack cellulose insulation, then clad with exterior moisture-resistant OSB sheathing (with taped joints). Advanced gasket technology is used for air sealing, detailing is provided to minimize thermal bridging, a drainage plane is installed on the exterior, and integral baseboard raceways are provided on the interior for electrical and data cables to eliminate wall penetrations for wiring. The computer modeling not only controls the exact design and fabrication of these wall panels, but even identifies the proper placement of nylon straps for hoisting the (heavy) modules into place on the jobsite. All this is done with a minimum of waste through material optimization and factory fabrication. OBPlusWall modules ship to the jobsite with windows installed and sometimes also with siding, though for some projects the builder chooses to handle more of the finish work on-site.
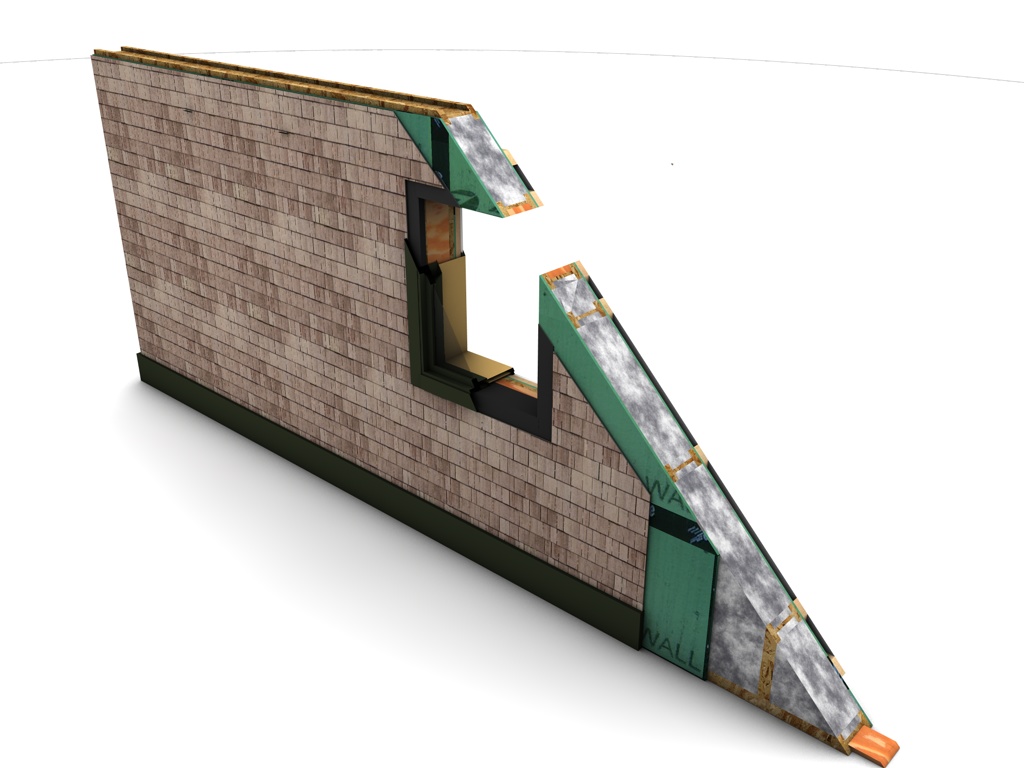
The companion to the R-35 wall system is a standard R-38 roof system, also insulated with cellulose. Where performance goals demand, Bensonwood can go a lot further with energy performance--by using deeper I-joists and including additional insulation components in the wall and roof systems. When I visited, the company was finishing a house designed to Passive House standards. This walls will have an additional 3.5 inches of cellulose on the interior and two inches of polyisocyanurate on the exterior, to achieve approximately R-60 performance. That project was slowed down because advanced Passive House windows took some time to arrive from Germany--one of the complications with creating state-of-the-art buildings today. Bensonwood creates premium homes with costs higher than that of typical tract homes, but the panelized construction allows the company to be cost-competitive with most custom homes today--while offering faster construction, better energy performance, excellent durability, and the addition of timber components to achieve Benson's signature elegance.
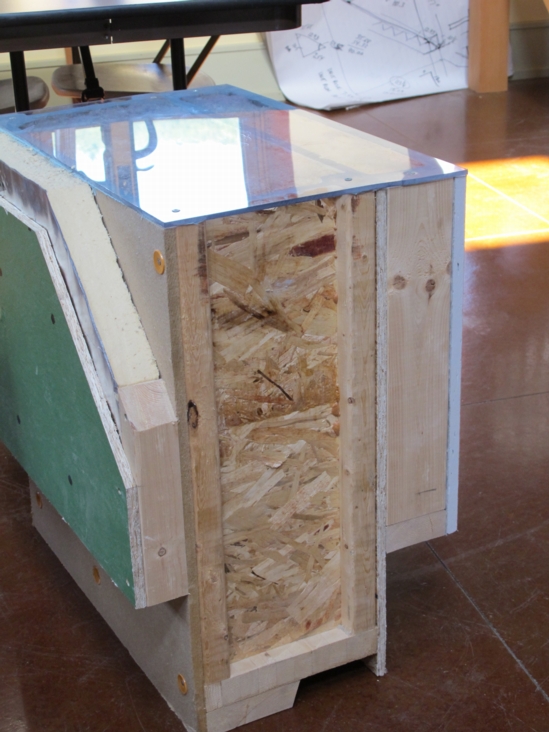
While Benson has been reinventing residential construction for more than 35 years, you wouldn't know it if you try to keep up with him on a bicycle! After my Bensonwood tour, he and I biked to Walpole for a beer--via a hilly circuit that Tedd uses to keep in shape on his lunchtime rides. It turns out he uses annual biking trips in the Alps to visit high-tech European manufacturers and software companies--some of the tools that keep Bensonwood ahead of the curve in today's quickly evolving building industry. In addition to this Energy Solutions blog, Alex writes the weekly blog on BuildingGreen.com: Alex's Cool Product of the Week, which profiles an interesting new green building product each week. You can sign up to receive notices of these blogs by e-mail--on any blog page enter your e-mail address in the upper right corner. Alex is founder of BuildingGreen, LLC and executive editor of Environmental Building News. To keep up with his latest articles and musings, you can sign up for his Twitter feed.
Published August 3, 2010 Permalink Citation
(2010, August 3). Bensonwood Reinventing the House. Retrieved from https://www.buildinggreen.com/blog/bensonwood-reinventing-house
Comments
Congratulations to him. Our
Congratulations to him. Our current methods, especially those used on custom homes, are as inefficient as can be imagined. Now if he'd drop that dorky 19th century wood look, he'd have something! ;-)
As an HVAC engineer I love OB
As an HVAC engineer I love OB. Finally there is enough room for ductwork and piping, and for changing things down the road. BensonWood has been getting very good blower door test results from their homes.
Plenty of people love the vis
Plenty of people love the visual characteristics and warmth of wood, modernists as well as traditionalists. What would you have him build with[INVALID]concrete? Bottom line: Tedd does beautiful and innovative work, and his understanding and appreciation of wood is a key factor in that. It's not only incorrect, but infantile to describe a style of building you happen to dislike as "dorky" because it references the building traditions of the previous few centuries.
Very nice invention, can we e
Very nice invention, can we expect to see this in commercializtion any time soon? I think this would be very attractive to green home builders.
This does sound like a nice s
This does sound like a nice system. Other articles I have read have noted concern regarding the potential for settling when shipping panelized walls with dense pack cellulose preinstalled at the factory. I know some German manufactures of ballon/Ijoist panelized walls install the cellulose at the site for this reason. Has Benson Wood found this not to be a concern or do they install the cellulose at the job site?
Steph, I think you missed Buz
Steph, I think you missed Buzz's wink at the end... his "dorky" comment was with tongue planted firmly in cheek, as far as I can tell!
Add new comment
To post a comment, you need to register for a BuildingGreen Basic membership (free) or login to your existing profile.